The CAPTOR radar family provides the main sensor for the Eurofighter Typhoon fighter aircraft. This article aims to provide a deeper insight into the first iteration: CAPTOR-M. This piece is the first part of a two-part series of articles. The second article focuses on the development and capability of the CAPTOR-E electronically steered radar.
Development History
In December 1983, France, Italy, Spain, West Germany and the U.K. collaborated on a new combat aircraft called the European Fighter Aircraft (EFA). In June 1985, discussions began between various corporations to explore the possibility of cooperation for the EFA’s radar. The United Kingdom selected Ferranti (now Leonardo) as the leading contractor, whereas Germany went with the firm AEG-Telefunken (now Hensoldt). Italy selected FIAR (now also Leonardo) to provide an Italian contribution. Spain, which had no notable experience in building fighter radars, only played a minor role initially.
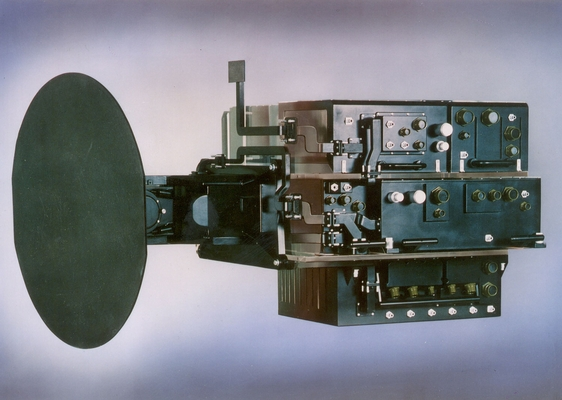
Towards the end of the same month, a memorandum of understanding was signed between the UK, Germany, France, Italy and Spain to work on a joint radar proposal for the EFA. At the time, France already stated its intent to withdraw from the EFA program. The French firm Thomson-CSF (now Thales) was thus faced with a dilemma, as the preferred choice within the company was to participate in the EFA radar project. Therefore, in 1987, Thomson-CSF begun negotiations with Ferranti to secure work share. Upon the official French withdrawal from the EFA program all negotiations to include French companies in the radar development were halted.
Ultimately two consortiums put forth their bids. The offers came from the leaders of the two consortiums: Ferranti (UK) and AEG (Germany) and were sent to the Eurofighter Jagdflugzeug GmbH upon completion. Ferranti had already presented its European Collaborative Radar 90 (ECR-90) proposal in 1986, a proposal based on the Blue Vixen radar of the Harrier fighter aircraft. AEG offered the MSD-2000 Emerald, which was to use the American AN/APG-65 radar as its basis. Both radars were to be produced by a consortium including companies from all partner nations. Both suppliers submitted two-part bids: One that fully complied with the Request For Proposal (RFP) and a less capable, low-cost variant.
After an extensive evaluation all offers were turned down by participating governments. Both high-tech offerings were too expensive, and the low-cost alternatives were judged to be too insufficient to meet baseline requirements. These unsatisfying circumstances led to a new initiative where both bidders were asked to submit reworked offers that were supposed to represent a compromise between the respective previous bids.
The decision making process in the following years from 1988 until 1990 mostly took place on the political level, revolving around the companies and governments of the United Kingdom and Germany trying to come to terms in order to make progress with the project. The most controversial issues included intellectual property rights, distribution of production share and increasing costs. To solve the gridlocked situation, the participating corporations took multiple steps of consolidation, notably GEC-Marconi merging with Ferranti and DASA (the successor firm of AEG-Telefunken) being offered a third of the production shares by GEC in order to join the ECR-90 consortium. These developments paved the way for the signing of the radar development agreement in early 1990, with the £300 Million developmental contract being awarded to GEC-Ferranti.
After the contract signature, the participating companies quickly moved ahead and formed the EuroRadar consortium. The workshare distribution was aligned accordingly to the entire Eurofighter project. 33% of the work packages were each assigned to the UK and Germany, 21% to Italy and the remaining 13% to Spain.
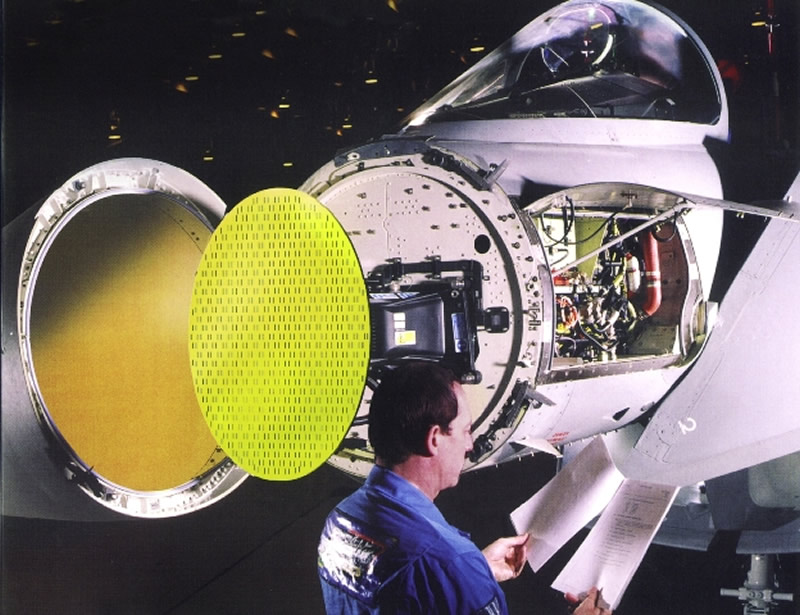
After the establishment of clear organisational structure and responsibilities, the participating companies promptly initiated the design process. Despite meeting the planned schedule at first, the pace of development was hindered by the restrictive funding situation caused by the end of the Cold War. Regardless of these issues, three years after the first contract signature, the initial ECR-90A radar was installed on a BAC 1-11 instrumented test aircraft, carrying out the first live, airborne tests of the radar.
The testing showed promising results at first but problems arose with the radar antenna and its interactions with the radome. The antenna’s emitted energy did not penetrate the radome correctly and thus an extensive redesign was initiated by DASA. After these issues were resolved, testing continued as scheduled with the new iteration of the system, now called ECR-90B.
The next milestone within the project was achieved in November 1996 when the German DA5 test aircraft first flew with an ECR-90 prototype. The data collected from the following tests with the aircraft were used to further develop the radar’s software. New processing with increased computing power were also added. These changes were incorporated into the ECR-90C version which was first tested on a live aircraft in 1999. This version marks the end of the pre-service development of the radar as the initial development was concluded in 2000.
The first production variant ECR-90C radar set was delivered in 2003, when the initial serial production Eurofighter was handed over. Coincidental to the first deliveries of the aircraft, the radar was also given a new naming scheme, adopting the use of the CAPTOR prefix.
General characteristics
The following section will describe the characteristics and performance of the mechanically steered versions of the radar: CAPTOR-C and CAPTOR-M. CAPTOR is a mechanical multi-mode pulse-Doppler radar operating in the X-Band (8-12GHz). The system weight is 193kg. The radar set is modular, combining six Line Replaceable Units (LRUs). The LRUs include the antenna, the transmitter unit, the radar processor, the receiver module, the antenna control unit and the antenna power supply. These in turn contain a total of 61 Shop Replaceable Items (SRIs). The instrumented range is configured at over 370 kilometers. The original variant of the radar can track up to 20 targets at once, while engaging eight of them simultaneously. The radar has two main mechanically scanned variants: CAPTOR-C is the original version, only fitted to Typhoons of the Tranche 1 production lot and CAPTOR-M is a later version fitted to Tranche 2 jets onwards. The two standards differ in both hardware and software.
Components
The German-made antenna is made of a carbon-fiber-reinforced polymer plate with horizontal polarization. It has a diameter of over 700 millimeters. The antenna surface is fitted with a large number of slots which are cut into the plate with high precision machinery. The general slot characteristics are dictated by the wavelength (λ) of the X-Band. Their approximate dimensions are ~1.5cm (approximately 0.5λ) in length and a diameter of ~2.5 millimeters (approximately 0.1λ).
The antenna assembly is coupled to four high torque 0.5hp samarium-cobalt motors which steer the antenna mechanically. These are controlled by the control unit. The steering works in the vertical and horizontal plane with electronic compensation of roll angles. The high scan rates generated by the servo motors allow for interleaved operation, quasi-simultaneously operating in modes like Synthetic Aperture Radar (SAR) mapping and Track While Scan (TWS) which is something usually only phased array radars are capable of.
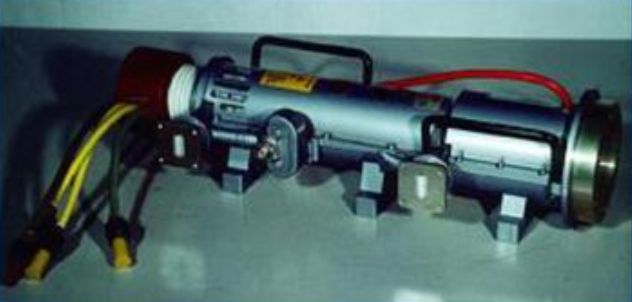
The energy radiated by the antenna is generated by the ET963 coupled cavity Traveling Wave Tube (TWT) made by Leonardo in Italy. The device is able to provide enough power for the radar to transmit at peak power levels above 9-10kW while operating at voltages of 30-50kV. The average transmit power is stated to be around 1-2kW. In order to manage emissions to stay in a Low Probability of Intercept (LPI) profile, the radiated power is kept as low as possible in the respective operating modes. The average mean time between failures (MTBF) is stated to be around 600 hours.
The digitized signals from the antennas are analysed in the receiver unit, a component jointly manufactured by Leonardo UK and Hensoldt in Germany. It has three distinct receiving channels, making it the first fighter radar in NATO to do so. Each of the channels has its own set of tasks: the first channel is assigned with target acquisition, the second channel is responsible for track management in both air and ground modes and the third data channel is employed for screening and classifying Electronic Warfare (EW) sources and suppression of side lobes, improving the radars electronic counter-countermeasures (ECCM) capacity. The ECCM channel also enables the radar to carry out jammer mapping, a function allowing the identification of EW threats that are targeting the aircraft.
These formatted signals are handed over to the radar processing unit. Like the receiver, the radar processor is also built in the United Kingdom and Germany. It is a digital computer complex making use of 32-bit architecture. It is responsible for extracting actionable information about the signal environment from the streamlined radar signals. The processor is responsible for creating trackfiles that store information based upon the collected target data. These trackfiles store all gathered data from the detected targets. In conjunction with Identification Friend and Foe (IFF) and Non Cooperative Target Recognition (NCTR), both friendly and enemy air targets are automatically identified. The NCTR process can be conducted in a few possible ways. One of the options makes use of so called Jet Engine Modulation (JEM). This function analyses the radar returns reflected by the target’s turbine blades. The collected data is correlated with an onboard database and added to the trackfile upon identification.
With the amalgamated information the processor partly manages the Antenna Control Unit and the Transmitter Auxiliary Unit for CAPTOR to operate under optimised conditions. This includes so-called Data Adaptive Scanning (DAS) which enables the radar to adjust the scan pattern to the current situation, avoiding unnecessary antenna movements and scan angles which also aids during the aforementioned interleaved operation. The TAU can provide a highly variable Pulse Repetition Frequency (PRF), switching ranges between low, medium, and high PRF. The pulse repetition frequencies range from 1000 to over 200 000 impulses per second. To exchange sensor fusion data with the other onboard sensors of the Eurofighter platform there is an interface to the Attack and Identification System (AIS) of the aircraft.
The LRU hardware is powered by standardized CPUs which are also used on other components of the Eurofighter. The processors found on the CAPTOR-C are of the 68020 series designed by Motorola. They were first marketed in the 1980s, thus providing inadequate performance in certain operating modes. The chips were later replaced with more modern PowerPC-4 processors for Tranche 2 (CAPTOR-M equipped) aircraft. The PowerPC CPU has found wide applications in other fighter aircraft as well, such as the F-35. The radar has seen a significant performance boost as a result of this hardware upgrade. A prime example to demonstrate the performance increase is the SAR mapping mode. The quality of the radar images has been improved from a 1-meter resolution down to 30 centimeters for CAPTOR-M.
Software
The software of the radar is written the Ada language, according to MIL STD 2167A. The CAPTOR-C software package was initially comprised of 1.2 million lines of code, making use of xUML during the coding process. To accommodate for future upgrades the radar LRUs were fitted with USB 2.0 ports for easy software adaptations. The first radar updates (R2P and R2Q) were installed in 2011 and 2012 respectively. The software was initially only found on Royal Air Force (RAF) Typhoons and was added to German aircraft later in the same year. The upgrades refined existing radar modes whilst also introducing new capabilities. Indra in Spain has also been active in an ongoing effort to modernize the CAPTOR-C radar sets on the Spanish Tranche 1 Eurofighters, narrowing the capability gap from the newer CAPTOR-M variant.
Modes of operation
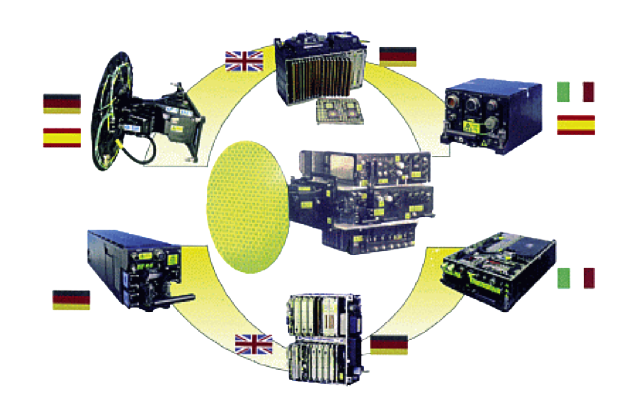
CAPTOR is a multi-mode radar with multiple air-to-air and air-to-ground modes. By default the onboard Attack and Identification System (AIS) of the Eurofighter selects the modes of operation depending on the overall sensor fusion picture. The pilot can operate the radar by the principle of Voice, Throttle & Stick (VTAS). During the initial design phase, the radar was required to feature at least 31 different modes. The operating modes available to CAPTOR-M fall into three basic classifications.
The main array of functions can be classified as useful for beyond-visual-range (BVR) engagements. These modes constitute the majority of the radar’s capability and represent the primary role of the system. The three main BVR modes are:
- Velocity Search (VS)
- Range While Search (RWS)
- Track While Scan (TWS)
Range While Scan serves as the primary search mode to track and acquire targets from long distances. A Single Target Track (STT) mode is also provided for this purpose to provide the most accurate tracking data to the Typhoon’s AIS so that accurate missile or gun firing can be accomplished. Using the Velocity Search mode, targets can be detected at very long distances but no range information is provided. Track While Scan, the primary search mode in the Eurofighter, allows multiple targets to be detected and tracked. These can be tracked by pilot-adjusted priorities. The radar also provides Look up/Look down or Shoot up/Shoot down capabilities. Multiple target engagement is also possible in Track While Scan mode. The Raid Assessment function is used to identify and detect targets flying close to each other. The area around a radar contact is scanned extensively so that even dense formations can be correctly assessed.
In addition to the various BVR modes and functions, CAPTOR also has the following modes for automatic acquisition of single targets in close air combat at visual ranges:
- Boresight Acquisition
- Vertical Acquisition
- Slaved Acquisition
- HUD Acquisition
In Boresight Acquisition mode, only a small circular area in front of the aircraft is scanned. When the pilot selects the Vertical Acquisition mode, the radar primarily scans vertically to acquire targets that are above the nose of the aircraft. The Slaved Acquisition mode correlates the radar’s scan direction with the helmet-mounted display’s direction, effectively steering the radar with the pilot’s head movement. In Head-Up-Display (HUD) Acquisition mode, the radar acquires targets that are within the bearings of the aircraft’s HUD.
During close air combat, once a target is acquired, the radar automatically switches to a single target tracking mode. Weapon engagement then is usually handled with the pilot’s helmet-mounted display system. In general, the air-to-air modes also provide data for weapon engagement. Among other things, CAPTOR also determines the optimal engagement window for the selected weapon.
Finally, the radar also has a range of air to surface modes including:
- Synthetic Aperture Radar (SAR)
- Ground Moving Target Indication/Track (GMTI/T)
- Naval Targeting
- Terrain Avoidance
- Ground Ranging
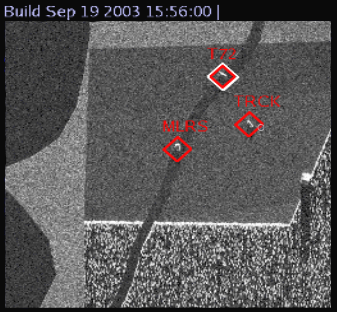
The Synthetic Aperture Radar function can be used to create radar maps and images at a high resolution of 30 centimeters. This allows surface objects to be detected and identified while facilitating navigation. Accurate tracking of both stationary and moving objects on the ground is enabled by the Ground Moving Target Indication/Track function. Identification of possible targets is aided by a built-in database that has various threat entries (such as tanks), providing the pilot with a type assessment. CAPTOR can thus also facilitate the engagement of possible targets such as fortifications, vehicles, or surface-to-air missile installations. To create situational awareness in the naval domain the radar features the Naval Targeting mode. In that mode, the radar searches for sea targets using multiple detection methods. Surface vessels can be detected and tracked at distances over 180 kilometers. With the Terrain Avoidance function, the radar can also display obstacles and provide timely warnings of them. The Precision Velocity Update and Ground ranging modes provide accurate environment measurements over the ground and feed data to the aircraft to update onboard navigation systems.
Future
As of 2023, 590 radar sets of the CAPTOR-M system have been delivered. Upgrades to the mechanically scanned variants are only likely in the fields of weapon integration or by way of additional software drops. It is likely that this number represents the final production amount of the radar. Although there are more Eurofighter aircraft being ordered, the newly built fighters are all set to receive radars of the more advanced CAPTOR-E AESA portfolio. An in-depth article on the newer AESA variants can soon be found here.